In recent years, the world of recycling has found itself faced with numerous challenges which have, however, at the same time created a series of new opportunities. For this reason, often the most correct term to identify the activities that companies like ours carry out on a daily basis is that of “research workshop”… a continuous search to find solutions that can solve a problem and generate new job opportunities.
In this research, all the experiences already made clearly come into play and are modeled, modified and reformulated to obtain a result that can be sustainable and convenient from an economic and environmental point of view.
Sometimes we encounter challenges that seem impossible, and in fact they are, other times they are just difficult and ultimately lead to important results.
To regenerate this product, a perfectly clean granule must be obtained, free of any impurities such as residues of textile fibres, metal or other.
With our densimetric separators this result is guaranteed and can be achieved in a streamlined and economical way with the work of a single machine.
The line of DM series separators is in fact capable of removing all those impurities that would otherwise make the ELT and EPDM rubber granule unusable or in any case of very poor quality.
Based on the result we want to obtain, we are not only able to remove impurities, but also to select a product with high density and therefore of very good quality, from one with lower density and therefore of poorer quality.
All this is possible thanks to the infinite work curves of the DM series separators specific for the recovery of ELTs and EPDMs, which in recent years have been giving us a lot of satisfaction, a confirmed fact especially from our customers who praise their ease of use and the product quality that they manage to obtain with their use.
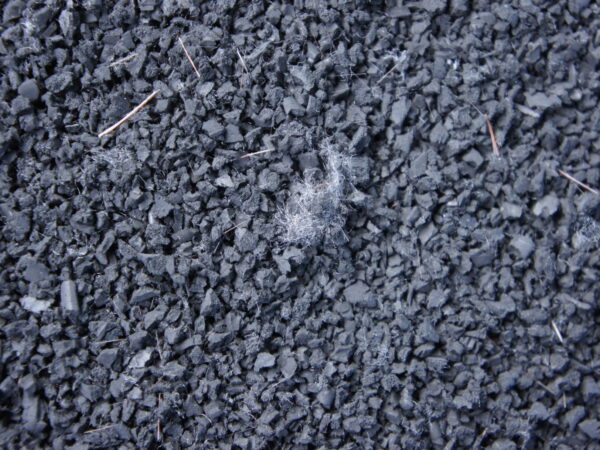

The DM150 Separator is suitable for granule flow rates to be cleaned ranging from 1500 to 2000 Kg/h depending on its size and specific weight.
The DM100 Separator is suitable for flow rates of granules to be cleaned varying from 1000 to 1500 Kg/h depending on the size and specific weight of the same, while as regards the DM50 it is often used by our customers in those cases in which they want to recover a part of low density powder or granule from the waste of a DM100 or DM150, or for small quantities of material to be sampled in the laboratory.
Thanks to the numerous installations of machines by GHIRARDUZZI in this sector, we can state that we have gained proven experience in the field of manufacturing machinery for the recycling of used tyres. The study and tests on the products that we do together with our customers are continuous; you can see the numerous videos of this separation process on our channel youtube.
If you still have doubts and want to personally verify the results that can be obtained, all you have to do is contact us to organize a test with your material, you will be welcome and you will be able to understand the simplicity of use of our separators and evaluate their degree of purity of product obtained, but above all of reliability.