Many materials can be transformed back into raw materials and reused for other purposes, avoiding unnecessary waste of resources and guaranteeing considerable savings.
Metals such as iron, steel, copper, brass, aluminium, nickel, palladium and cobalt are continuously recycled to be used again in industry and technological research.
The metal recycling process involves multiple processing phases that adopt different technologies.
The main processing phases can be considered common to most of the recovery processes of different metals, in particular for those of greatest interest in terms of quantity and value.
The different technologies are however based on mechanical treatments aimed initially at the volumetric reduction and primary separation of the different components, and subsequently integrated by applications for the recognition and separation of foreign bodies, different fractions, considered “pollutants”. These are technological applications such as gravitational systems, eddy current, screens, magnetic separators, etc. increasingly widespread both due to the growing interest of the legislator towards the circular economy, and due to the greater economic value of the treated scrap and the ever-increasing costs of waste disposal.
To properly dispose of old scrap, meticulous separation of the metal parts is necessary. Ferrous metals such as steel are isolated through the use of magnets, other metals such as aluminum are instead separated using densimetric separators which recognize the lower specific weight compared to other metals.
Italy is a country at the forefront in the reuse of metals and alloys, as demonstrated by the excellent results obtained in many related sectors, including aluminum packaging. Cial (Aluminium Packaging Consortium) has estimated that 70% of the raw materials introduced into the market are recycled to take on new forms depending on the industrial sector of destination.
Thanks to this possibility of recovering and reusing metals and ferrous scrap it is possible to cover the raw material needs of the steel industry and of all those production sectors that use metals or alloys. Recycling allows us to reduce the exploitation of raw materials in mineral form, ensuring significant savings in resources which can therefore be invested in research and technological development.
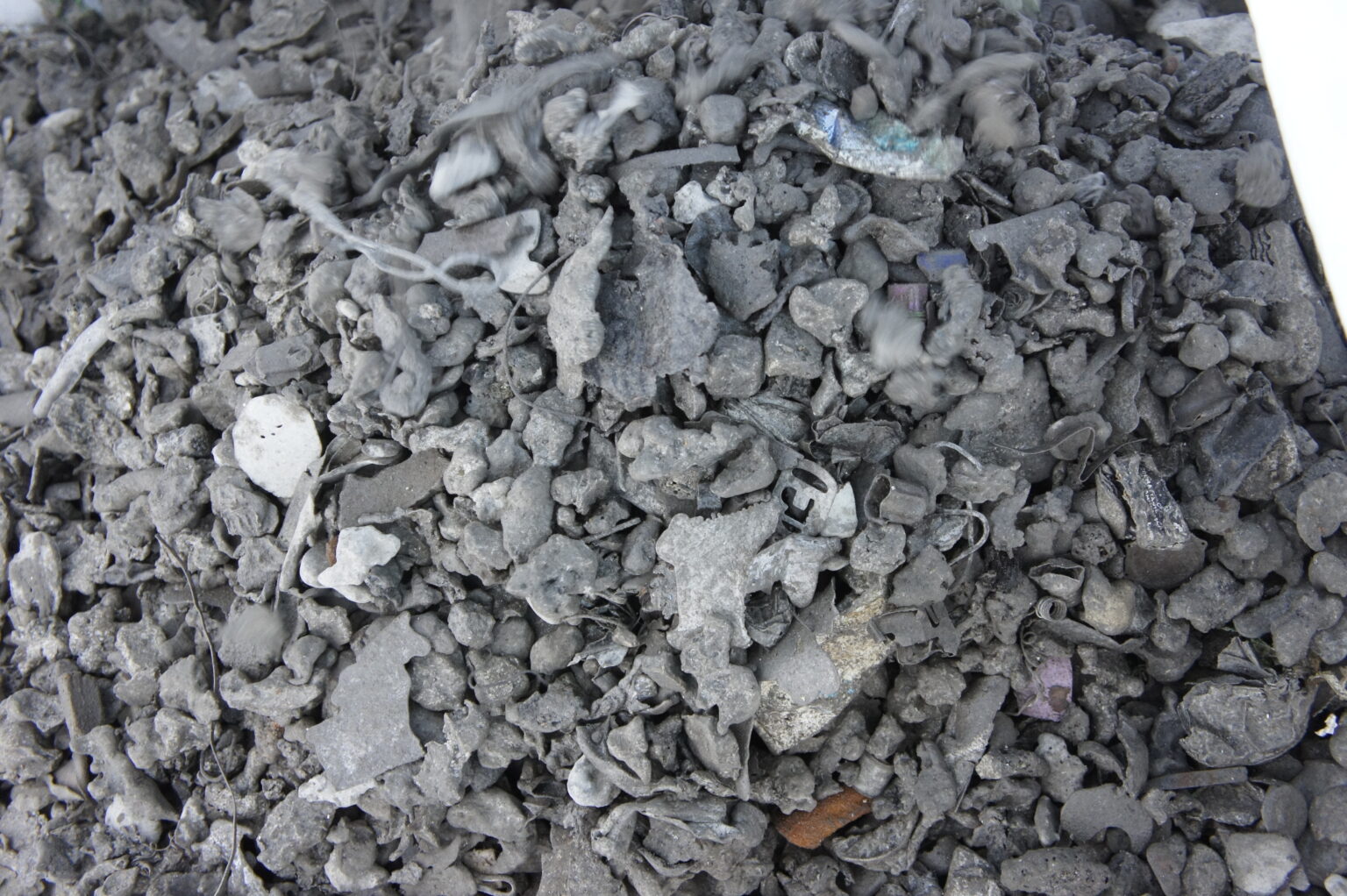
The growing increase in the cost of landfill disposal in recent years has made waste recovery increasingly interesting from an economic point of view. The most applied treatments range from the simple recovery of the metals contained therein, to the reuse of the inert material in road surfaces or as an additive in the production of cement or construction materials.
The use of these bottom ashes is conditioned by the presence of heavy metals within them, the removal of which leads to a double benefit: extracting salable metals and at the same time avoiding the costs of landfilling.
The inert material obtained from the treatment of slag can be used as a raw material for the preparation of raw flour fed into the cement kiln only after removing the ferrous and non-ferrous metals. With these recoveries, ceramic materials, glass fibers, filling material and road paving are manufactured.
To get an idea of the economic value, it must be considered that on average slag contains approximately 7-15% ferrous metals and 1-2% non-ferrous metals. In particular, non-ferrous metals are composed mostly of aluminum (more than 60%) with a smaller percentage of other precious metals such as brass and copper.
In this regard, the Ghirarduzzi company produces separators to separate the whole part from the metallic fractionstill present in the slag or ash.
You can contact us for more information, as well as to request a process test directly on a sample of your material.