The sustainable management of End-of-Life Tires (ELTs) currently plays a crucial role in the most advanced economies, both to support environmental protection and to promote the development of a circular economy in this sector. Through recovery and recycling processes, it is indeed possible to reduce the ecological impact of improper disposal, limit harmful emissions, and give new life to materials by transforming them into valuable resources for various industrial sectors.
Once they reach the end of their life cycle, all tires can be recycled to recover highly valuable materials such as rubber, steel, and even textile fibers.
The effective separation of textile fibers from rubber is an important step in this process, as it improves the quality of recycled materials and expands their reuse possibilities.
The ELT Recycling Process
The recycling of ELTs begins with a series of phases aimed at separating the different components of the tire:
- Shredding: Tires are reduced into fragments of varying sizes through mechanical grinding at ambient temperature.
- Granulation: The fragments are further reduced into smaller granules, facilitating the separation of components.
- Separation: In this phase, rubber is separated from steel and textile fibers. The recycled rubber can be used in various sectors, while the steel is recovered for reuse in foundries.
Technologies for Cleaning Textile Fibers
The textile fiber extracted from ELTs often retains rubber particles, which can reduce the quality of the recycled material. However, to address this type of issue, specific treatment systems have been studied and developed.
Ghirarduzzi srl, an Italian company specialized in the design and construction of recycling and material separation systems, has over the years studied, designed, and developed innovative solutions for separating textile fibers from rubber in the recovery processes of End-of-Life Tires (ELTs).
Technologies and Processes Implemented by Ghirarduzzi
To tackle the challenge of effective separation of textile fibers from rubber, Ghirarduzzi has introduced a dedicated separation line for rubber granules derived from the recovery of ELTs and EPDM. This line has been specifically designed to remove impurities that could compromise the quality of the recycled rubber granules.
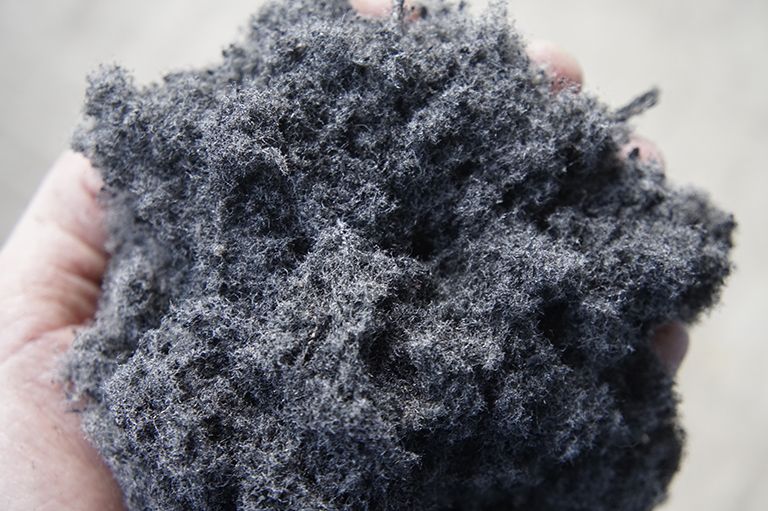
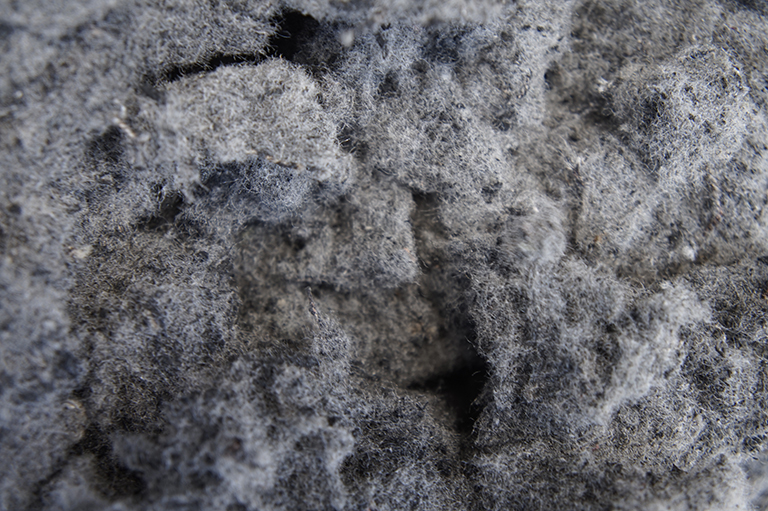
A key component of this line is the TFC 100 pre-separator, which is responsible for removing a significant portion of the textile fiber present in the incoming material.
This process begins by creating a compact bundle of fibers, leaving the rubber granule partially cleaned. The next phase involves the use of the DM series densimetric separator, which completes the cleaning of the granule, ensuring a final product of the highest quality.
The DM150 separator, in particular, has been designed to handle specific grain sizes, such as 0.8–4 mm rubber granules, effectively separating them from residual textile fiber.
This process uses densimetric separation to distinguish clean granules from powder and textile fibers, ensuring a final product that meets the standards required by the recycling industry.
Advantages of Ghirarduzzi Solutions
The technologies developed by Ghirarduzzi offer several advantages in the PFU recycling process:
- Granule Quality: The effective removal of textile fibers and other impurities ensures a high-purity rubber granule, expanding its potential reuse in various industrial sectors.
- Operational Efficiency: The integration of pre-separators and densimetric separators optimizes the cleaning process, reducing both time and operational costs.
- Flexibility: Ghirarduzzi solutions can be adapted to different production needs, handling various types of materials and grain sizes.
The TFC100 pre-separator, introduced at the end of the cycle, ensures the complete removal of rubber dust and rubber residues from the textile fiber, thus converting what is currently considered waste into a secondary raw material that can be used for higher-end purposes.
A significant example in this field is the REFIBRE project, funded by the European Community under the LIFE programme. The aim of the project was to develop a plant capable of transforming textile fibers derived from PFUs into pellets, making them dosable and usable in new production processes. This pelletization process allows the fibers to be compressed, reducing their volume and facilitating transportation and storage, paving the way for new industrial applications.
- Reinforced Asphalt Production: Integrating textile fibers into asphalt can improve the mechanical properties of road surfaces, increasing their strength and durability.
- Composite Materials: The fibers can be used to produce lightweight and durable composite materials, suitable for sectors such as construction and automotive.
- Thermal and Acoustic Insulators: Thanks to their intrinsic properties, recycled textile fibers can be transformed into insulating panels for buildings, contributing to energy efficiency.
In conclusion, we can affirm that the transformation of textile fibers from waste to secondary raw materials in PFU recovery represents an important step forward towards more sustainable waste management and the concrete implementation of the circular economy. Projects like REFIBRE demonstrate how technological innovation can create new opportunities for materials previously considered waste, helping reduce environmental impact and enhance resource value.
The company GHIRARDUZZI, always attentive to innovation and research, offers for this challenge the TFC100 pre-separator, which, placed both upstream and downstream of the recovery line, ensures maximum cleaning of the granule and textile fiber, thus opening up new horizons for higher-end and more refined applications compared to the current use of this material.
For more information on this type of separation, visit our YouTube channel:
https://www.youtube.com/watch?v=qEI_9k-fwPk